A horizontal vibrating screen is a type of screen that uses a horizontal oscillating motion to move material across the screen surface. It is commonly used in the process of screening bulk materials such as aggregates, coal, minerals, and other materials. The primary purpose of a vibrating screen is to separate and classify particles based on size.
Horizontal vibrating screen components

Screen Deck: The screen deck is the surface where the material is placed for screening. It typically consists of multiple layers or levels of screens with different-sized openings.
Vibration Mechanism: Horizontal vibrating screens use a horizontal, linear motion to move material along the screen deck. This motion is generated by an unbalanced eccentric shaft or electric motor that imparts a vibrating force to the screen box.
Screening Media: The screening media, such as wire mesh, polyurethane, or rubber panels, is responsible for separating particles based on their size. The choice of screening media depends on the specific application and the characteristics of the material being screened.
Drive Unit: The drive unit consists of the motor and other components that generate the vibrating motion. It can be positioned at one end of the screen or in the center, depending on the design of the vibrating screen.
Support Structure: The screen is supported by a sturdy frame or structure that provides stability and allows for proper installation.
Horizontal vibrating screen working principle
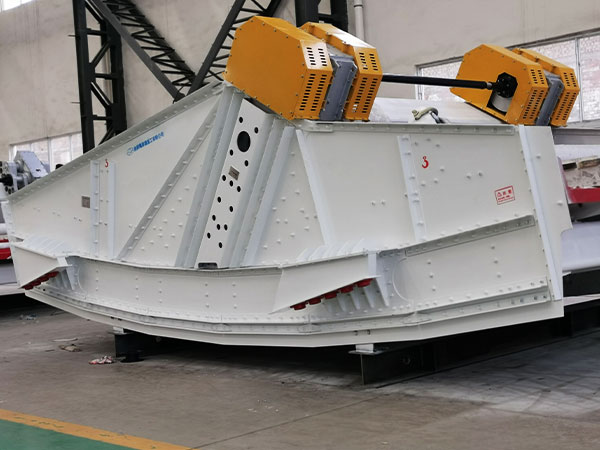
A horizontal vibrating screen is a type of mechanical equipment that uses a horizontal motion to perform its screening operation. The working principle of a horizontal vibrating screen involves the following key elements.
Screen Deck: The screen deck is the surface where the material to be screened is placed. It can be made of various materials, and the choice depends on the application and the type of material being processed.
Vibrating Motor or Exciter: Horizontal vibrating screens are equipped with one or more vibrating motors or exciters. These motors generate the vibratory motion needed for the screening process. The motors are usually positioned on the sides of the screen and connected to the screen deck.
Eccentric Weights: The vibrating motors have eccentric weights attached to them. The placement of these weights creates an unbalanced force, resulting in a circular motion or vibration. The eccentric weights are often adjustable, allowing for fine-tuning of the screen’s performance.
Screening Motion: The vibrating motion generated by the eccentric weights causes the material on the screen deck to move. In a horizontal vibrating screen, the material moves horizontally across the screen deck. This horizontal movement helps to efficiently separate and classify the particles based on their size.
Screening Surface Openings: The screening surface contains openings or perforations of a specific size. Smaller particles pass through these openings, while larger particles are retained on the screen. The size and shape of the openings can be customized based on the desired end product.
Inclination Angle: The screen deck is often set at a slight angle to facilitate the movement of the material. The inclination angle can be adjusted to optimize the screening process for specific materials and conditions.
Support Structure: The vibrating screen is supported by a robust frame or support structure. This structure is designed to withstand the dynamic forces generated during the screening operation.
Drive System: The drive system powers the vibrating motors and may include a belt drive, direct drive, or other mechanisms to transmit power efficiently.
Adjustability: Horizontal vibrating screens are often designed with adjustable parameters, such as vibration amplitude, frequency, and screen inclination. These adjustments allow operators to optimize the screening process for different materials and operating conditions.
Application
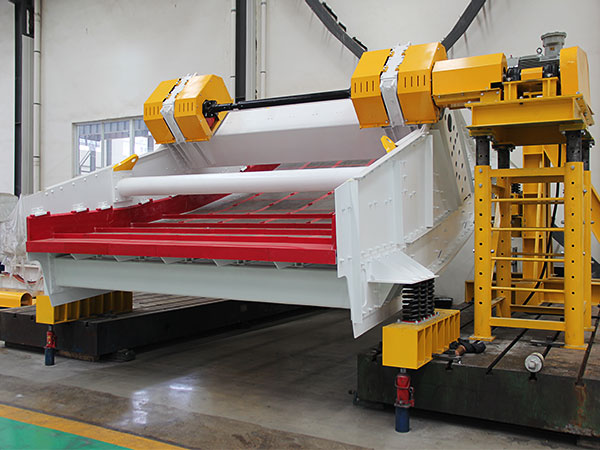
Horizontal vibrating screens are commonly used in a variety of industrial applications for the screening and grading of bulk materials. These screens operate by employing a linear motion horizontal deck configuration, which allows for efficient and effective screening of materials.
Aggregate Processing:
Separation and sizing of various types of aggregates, such as gravel, sand, and crushed stone, in the construction industry.
Mining Operations:
Screening and classifying minerals and ores in mining processes. Vibrating screens are used to separate valuable minerals from unwanted materials.
Recycling:
Sorting and classifying recycled materials, such as construction and demolition waste, concrete, and asphalt.
Sand and Gravel Industry:
Separation of sand and gravel for various construction applications, including concrete production and road building.
Coal Handling:
Sizing and sorting coal particles in coal processing plants. Vibrating screens are used to separate coal into different grades based on particle size.
Iron and Steel Industry:
Screening of iron ore and other raw materials in the production of steel.
Chemical Processing:
Screening and classifying chemicals and raw materials in chemical manufacturing processes.
Food Processing:
Separation and grading of food products, such as grains, cereals, and other bulk materials in the food industry.
Pharmaceuticals:
Screening of pharmaceutical powders and granules to ensure product quality.
Water Treatment:
Separation of solids from liquids in water treatment plants, including removal of debris and screening of wastewater.
Pulp and Paper Industry:
Screening of wood chips, pulp, and other materials in the paper manufacturing process.
Ceramics and Glass Industry:
Sizing and grading of ceramic powders and glass materials.
The above is all about the horizontal vibrating screen. The key advantages of horizontal vibrating screens include their ability to handle a wide range of materials, high efficiency in screening, ease of maintenance, and relatively simple design. These screens are versatile and can be customized based on the specific requirements of the application. The horizontal motion ensures effective material conveyance and screening across the entire width of the screen deck.