There are many types of vibrating screens and a wide range of applications. No matter what kind of screening equipment, the screen is an indispensable part. The sieve plate separates materials of different sizes under the action of vibration force through materials of different shapes and sizes, and material sizes, to achieve the purpose of classification.
However, the sieve plate is in direct contact with the material and will suffer a certain amount of wear from the material. Therefore, the sieve plate should have sufficient strength, high open rate and not easy to block holes.
The advantages and disadvantages of commonly used sieve plates for vibrating screens

1. Polyurethane screen
The all-urethane sieve plate is welded by a flat steel frame. The frame tooling is a design difficulty. It is a new type of fine selection product. In recent years, it has gradually replaced the stainless steel sieve plate. The all-polyurethane screen is mainly suitable for grading, dewatering, screening and other places such as coal mines, iron ore, copper mines, gold mines, etc. It is a necessary part of the vibrating screen. Because the sieve plate is used under very harsh conditions, it requires corrosion resistance, abrasion resistance, and aging resistance, so the size of the sieve slot should be small enough during use.
Advantages: polyurethane has high wear resistance, high elasticity, sound absorption, shock absorption, not easy to run rough, good wear resistance, long service life, high screening quality, strong self-cleaning ability, good screen penetration performance, noise reduction, and improved operating environment. Wide application range, etc.
Disadvantages: The product dimensions are not flexible and the production cost is high.
Selection principle: dehydration, de-intermediation and de-sliming of various linear vibrating screens.
2. Woven mesh screen
The woven mesh sieve plate is woven with metal wires with bent buckles, and the shape of the sieve holes is square or rectangular. The woven mesh screen has two types: coarse holes and fine holes. Coarse-hole woven screens are made of low-carbon structural steel wire, spring steel wire and stainless steel wire. Fine mesh woven nets are generally made of low-carbon steel, brass, tin, tin-copper and stainless steel, etc., and are woven with a special weaving machine.
Advantages: light weight, high opening rate; and in the screening process, due to the elasticity of the metal wire, high-frequency vibration will cause the fine-grained materials stuck on the steel wire to fall off, thereby improving the screening efficiency. Suitable for screening of medium and fine-grained materials.
Disadvantages: shorter life span.
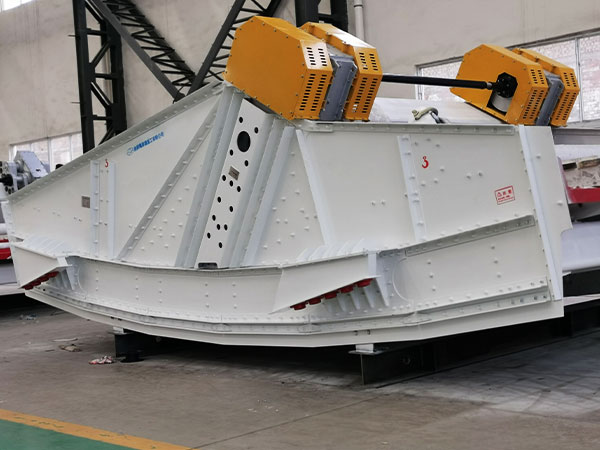
3. Stainless steel polyurethane composite screen
The stainless steel polyurethane composite sieve plate of this new technology is pressed into a wedge-shaped wire from stainless steel round wire, and is welded with the stainless steel convex support rib by the thermoplastic roller resistance welding process or the argon arc welding process. The frame is also vulcanized with polyurethane material, convex The support ribs replace the stainless steel convex wire part, and the process of welding the support ribs during assembly is also omitted. The outer frame is made according to the needs of users.
Advantages: high overall rigidity, low magnetism, sound absorption, shock absorption, not easy to run thick, easy to disassemble, especially suitable for the dehydration operation of heavy medium coal preparation plants.
Disadvantages: The production process is complex, the technology is relatively weak, and the quality is not easy to guarantee. In the drum resistance welding spin welding, the convex support ribs are easy to be welded, which affects the product quality and appearance, the production cost is high, and it is not easy to level, and the leveling effect is not satisfactory. . There are relatively few manufacturers with this process, and it is difficult to promote and apply it.
Selection principle: dehydration and de-intermediation of banana sieve.
4. Welded slotted screen
The welded seam sieve plate is a mature and old-fashioned sieve plate. It is mainly composed of stainless steel mesh sheets and stainless steel flat iron or carbon steel flat iron material frame assembly welding. The welding of stainless steel mesh sheets It is welded by a roller resistance welding machine, using rolled wedge screen strips and convex back strips of different cross-sections and the same cross-section, which are welded by resistance heat and current, which belongs to the contact resistance welding process.
Advantages: The working surface has high rigidity, narrow screen bars can be selected, high opening rate, flexible size change, and easy processing and forming.
Disadvantages: high noise, easy to run rough, not easy to disassemble, and poor surface abrasion resistance and anti-smashing performance during work.
Selection principle: dehydration, de-intermediation and de-sliming of various linear vibrating screens and slime curved screens.
5. Bar sieve plate
The bar screen is composed of a group of parallel steel bars with a certain cross-sectional shape. The bars are arranged in parallel, and the interval between the bars is the size of the mesh. The bar screen is generally used for fixed screens or heavy-duty vibrating screens, suitable for screening coarse-grained materials with a particle size greater than 50mm.
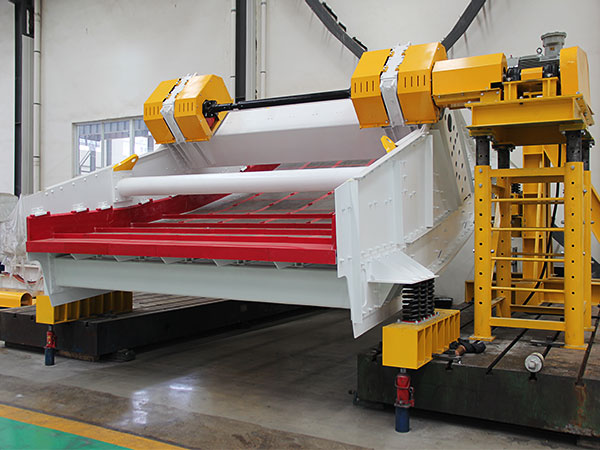
6. Polyurethane composite screen
Polyurethane composite sieve plate is a drum resistance welding machine that uses electrical current through the contact surface of the weldment joint and the adjacent area to generate the resistance heat energy to heat the welded metal to a local melting or high plastic state, and then use external force to weld it into a screen. The surface is assembled and processed to make it firm. On this basis, the frame is vulcanized with polyurethane material.
Advantages: Narrow screen can be selected, high opening rate, sound absorption, shock absorption, not easy to run thick, easy to disassemble and assemble.
Disadvantages: low screening rate, hole blocking, easy breakage of the screen, easy to wear, large particles of ore are easy to run out after wear, and the use value will be lost after wear or fracture, which indirectly causes high cost and inconvenient operation and maintenance. This kind of screen plate It can be produced by many domestic manufacturers in Taiyuan and Anhui, and it is easy to promote.
Selection principle: dehydration, de-intermediation and de-sliming of various linear vibrating screens and slime curved screens.
7. Punching sieve plate
Punching screens are generally formed by punching round, square or rectangular screen holes on a steel plate with a thickness of 5-12mm. Compared with the round or square sieve plate, the rectangular sieve has a larger effective area, lighter weight, and higher productivity. It is suitable for processing materials with higher moisture content, but the separation accuracy of sieving is poor.
The above is an introduction to the advantages and disadvantages of commonly used sieve plates for vibrating screens. The sieve plate is an important working part of the vibrating screen to complete the process of screening materials. Different materials and different places should choose different sieve plates to achieve the ideal screening. Effect. Under the premise of meeting the production process indicators, choose the sieve plate that is suitable for your actual situation and cost-effective, so as to create greater economic benefits.