Vibrating screen is an important screening equipment in mining equipment. After the material is screened by the vibrating screen, the specifications are clearer and the quality is higher, so its work efficiency affects the benefit of the entire production line. Therefore, it is also very important to choose a suitable vibrating machine, but some novice users may not know how to choose a vibrating screen. Below, the editor of Hiside will summarize a few selection points to teach you how to choose the right one.
Choose according to material characteristics
Each material that needs to be screened has its own unique properties, so choose a vibrating screen suitable for screening the material according to the different properties of the material. These attributes include: density, shape, temperature, viscosity, particle size, mobility, particle size distribution, corrosiveness, etc. According to your different materials, you need to choose different vibrating screens. If you are not sure about this, you can ask the manufacturer’s technicians to help you.
Choose according to processing capacity
1. When the required processing capacity is small, some light linear vibrating screens are cheaper and meet the demand; when the required processing capacity is large, a steel frame is required to ensure the quality. The steel frame of the mine linear vibrating screen can meet the requirements.
2. According to the size of the vibrating screen and the rated processing capacity, select a vibrating motor or a vibrating exciter of appropriate power.
3. Choose different sieve plate angles according to the nature of the material and the processing capacity requirements.
Choose according to the structure of the screen
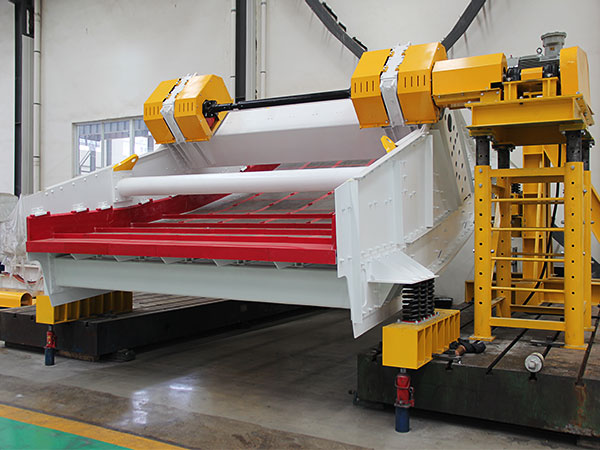
When selecting a vibrating screen, the screen area and number of layers, the shape, size and area rate of the screen hole, as well as the motion mode of the vibrating screen, the vibration frequency and amplitude and other factors should also be considered when selecting the vibrating screen. The screening efficiency of the vibrating screen is related to the movement form of the screen surface, so the screening efficiency of the fixed screen is relatively low, and the screening efficiency of the moving screen is relatively high. For the moving screen, the vibration of particles on the screen surface close to the vertical screen hole direction has a high vibration frequency and a better screening effect; if the particles slide in the direction of the screen surface, the screening effect is relatively poor.
Choose according to the screening purpose
According to different screening purposes, different types of vibrating screens need to be selected, such as: materials need to be pre-screened, generally linear vibrating screens; for grading and screening of crushed materials, large-scale vibrating screens, probability screens, etc.; for materials For de-intermediation and dewatering, it is better to choose a dewatering vibrating screen.
According to the production site selection
According to the customer’s production site, choose the right size vibrating screen. Technicians need to measure the site on the spot and need to ensure that the linear vibrating screen can be placed in the production line. The more basic is the length, width, and height of the vibrating screen, and the measured values must be accurate, otherwise the vibrating screen produced cannot be placed on the site. The vibration motor and exciter can be placed in different places (bottom or both sides) according to the actual site conditions. In this regard, we must choose a good manufacturer, because to ensure the power of Zhenyuan, Hiside Heavy Industry has rich experience and a large number of talents in the technical department, so it is worth choosing. The excitation force produced by bad manufacturers may not meet the amplitude requirements, which affects production. In addition to the length, width, and height, different shapes of inlet and outlet must be designed according to the production line, such as round and square.
other selection elements
1. Easy to repair. Try to choose models that are easy to maintain under the same conditions. Mine vibrating screens are basically open-air operations, and the processed materials are all mineral materials. The harsh production environment is likely to cause large and small failures in the screen. The easy-to-repair screen can effectively save maintenance time and cost.
2. Parts and components. All parts and components of the selected models should be standardized and serialized. In this way, when replacing damaged parts, it can be directly replaced without modification and debugging.
3. Security. The selected mine vibrating screen model must ensure the safety of production. Safety in production is more important than Mount Tai, and you must not use unqualified models and accessories to save purchase costs or maintenance costs.
The above is an introduction on how to choose a vibrating screen. The vibrating screen is one of the indispensable equipment in the mining production line. The correct choice can help increase productivity. It can be selected according to the characteristics of the material, such as shape, particle size, density, etc.; Selection of processing capacity; selection according to the structure of the screen, such as screen area, number of layers, etc.; selection according to six aspects such as the selection of screening purposes. Choosing a vibrating screen requires a lot of experience accumulation. Heside has been engaged in the development and production of vibrating screens for many years, and has solved various problems for customers. Therefore, if you buy a linear vibrating screen, you are welcome to choose Heside.