The capacity of a vibrating screen is a measure of the amount of material that can be processed or screened in a given time period. It is usually expressed as tons per hour (tph) or cubic meters per hour (m³/h), depending on the unit of measurement used. The capacity of a vibrating screen depends on several factors, including:
Screen Size and Surface Area: Larger screens and greater surface areas can handle more material.
Screen Deck Configuration: The number of decks on a vibrating screen can affect its capacity. Multiple decks allow for the sorting of different particle sizes.
Screen Motion: The type of motion of the vibrating screen, such as linear, circular, or elliptical, can impact its capacity. Different motions are suitable for different types of applications.
Screen Slope: The angle of the screen deck also plays a role. Steeper slopes generally allow for better material separation but can reduce capacity.
Material Characteristics: The type, size, and characteristics of the material being screened influence the capacity. For example, wet or sticky materials may require a different type of screen or additional equipment for effective screening.
Vibration Frequency and Amplitude: The frequency (cycles per minute) and amplitude (the height of the vibrating motion) can be adjusted to optimize the screening process for different materials.
Feed Rate: The rate at which material is fed onto the screen affects the screening capacity. Proper feed rates help ensure optimal performance.
Screening Efficiency: The efficiency of the screening process also affects capacity. Higher efficiency means more effective screening and potentially higher throughput.
Vibrating screen capacity calculation
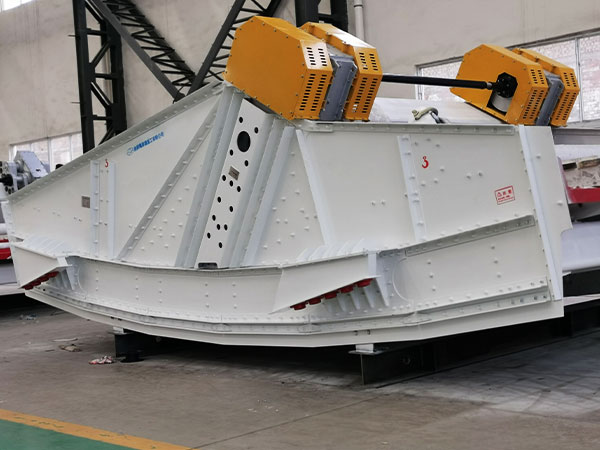
The capacity of a vibrating screen is typically represented by the throughput or the flow rate of material through the screen. The capacity calculation depends on various factors, including the screen dimensions, screen inclination, and the characteristics of the material being screened. Here’s a general approach to calculating the capacity of a vibrating screen:
1. Basic Formula:
The basic formula for calculating the capacity of a vibrating screen is:
Q=A⋅V⋅S⋅η⋅K
Where:
- Q is the capacity (throughput) in tons per hour.
- A is the effective screening area (in square feet).
- V is the percentage of material in the feed to the screen that is smaller than the screen opening size.
- S is the basic capacity of the screen in tons per hour per square foot.
- η is the efficiency factor, which is typically in the range of 90-95%.
- K is a correction factor that depends on the type of screen and the material being screened.
2. Effective Screening Area (A):
The effective screening area (A) can be calculated using the formula:
A=W⋅L/4
Where:
- W is the width of the screen in feet.
- L is the length of the screen in feet.
Basic Capacity (S):
The basic capacity (S) is calculated based on the opening size of the screen. The formula for basic capacity is:
S=V⋅(1−100/V)/100
Where:
- V is the percentage of material in the feed that is smaller than the screen opening size.
4. Efficiency Factor (η):
The efficiency factor (η) is an empirical factor that takes into account factors such as screen length, inclination, material moisture, and other conditions. It is typically determined through experience or testing.
5. Correction Factor (K):
The correction factor (K) is used to account for factors specific to the type of screen and the material being screened.
Example:
Let’s say you have a vibrating screen with a width (W) of 6 feet, a length (L) of 16 feet, and you are screening a material where 80% of the feed (V) is smaller than the screen opening size.
A=6*16/4=24 square feet
S=80*(1-0.8)/100=0.16
Assuming =90%η=90% and =1K=1 for simplicity:
Q=24*0.16*90*1=3.456 tons per hour
How to increase vibrating screen capacity
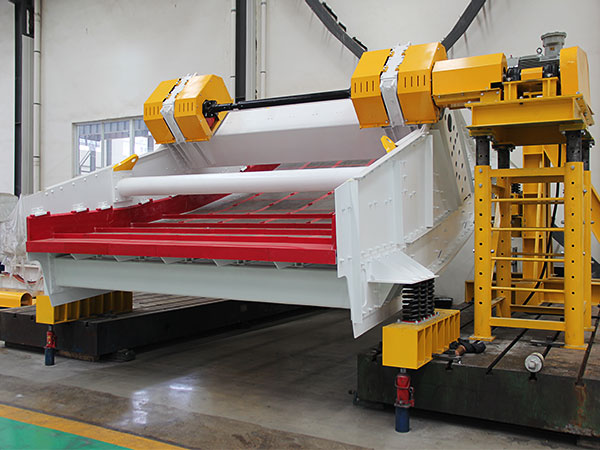
Increasing the capacity of a vibrating screen involves optimizing various factors related to its design, operation, and maintenance. Here are some general tips that can help you improve the capacity of a vibrating screen:
Screen Surface Area:
Increase the surface area of the screen. This can be achieved by using a larger screen or adding additional screen decks.
Screen Opening Size:
Use larger screen openings. Increasing the size of the openings in the screen panels allows more material to pass through, increasing capacity.
Screen Inclination:
Adjust the angle of the screen. Increasing the inclination of the screen can improve the material flow and help prevent material from building up on the screen.
Vibration Amplitude:
Increase the vibration amplitude. Higher vibration amplitudes help to convey material more effectively across the screen.
Vibration Frequency:
Adjust the vibration frequency. Experiment with different vibration frequencies to find the optimal setting for your specific application.
Screen Deck Configuration:
Consider using multiple screen decks. Multi-deck screens allow for the separation of material into different size fractions, increasing overall capacity.
Feed Rate:
Optimize the feed rate. Ensure that the material is fed onto the screen at a consistent and appropriate rate to maximize processing efficiency.
Screen Cleaning:
Keep the screen clean. Regularly inspect and clean the screen panels to prevent blinding or clogging, which can reduce capacity.
Screen Panel Material:
Choose the right screen panel material. Different materials have different wear and abrasion resistance properties. Selecting the appropriate material can extend the life of the screen and maintain capacity.
Vibration Mechanism:
Ensure the vibration mechanism is in good condition. Regular maintenance and inspection of the vibration mechanism, including motors and bearings, can prevent issues that might reduce performance.
Screening Media:
Experiment with different types of screening media, such as woven wire, polyurethane, or rubber panels. The choice of screening media can affect capacity and efficiency.
Deck Tensioning:
Ensure proper tensioning of screen decks. Tensioning the screen panels correctly helps maintain their integrity and prevents sagging or premature wear.
The above is about the influencing factors of vibrating screen capacity, how to improve production capacity and production capacity calculation. I hope it can be helpful to everyone and improve its production efficiency to a certain extent.