Izikrini zokudlidliza komugqa zivame ukusetshenziselwa imisebenzi yokuqeda amandla nokususa amanzi ezitshalweni zokulungiselela amalahle. Zisetshenziselwa ikakhulukazi ukusebenza kwe-de-intermediation kanye nokususa amanzi ezitshalweni zokulungiselela amalahle.
There are many types of structure and transmission methods for linear vibrating screens, such as flexible connection, universal joint shaft connection, etc. The excitation methods include eccentric sliders, box-type vibration exciters and other forms. This article mainly introduces the current compact structure Regular operation and maintenance of linear vibrating screen in the form of box-type vibration exciter.
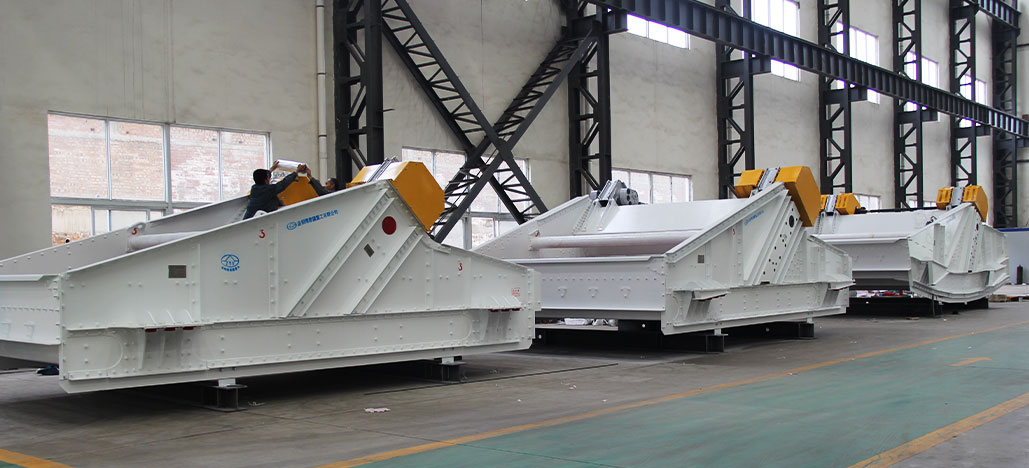
1. Main components of linear vibrating screen
1. Screen body: usually adopt ring-groove rivets to clean and seal assembly to avoid the corrosion of the bolt joint surface by wet objects. At the same time, the side panels are assembled without welding seams and rivets hydraulically to ensure that the overall structure has no residual stress.
2. Vibration beam: usually a box-shaped design, the main welds are fully penetrated, first-level UT inspection and magnetic particle inspection, and heat treatment to eliminate welding stress to ensure high strength. Before assembling, the mating surface of the excitation beam is precisely processed by CNC machine tools, which effectively guarantees the overall assembly quality of the screen.
3. Crossbeam: Usually circular special pipe design is adopted, and the main welds are all penetrated. First-level UT inspection and magnetic particle inspection are carried out, and heat treatment is carried out to eliminate welding stress and ensure strength. The surface can be treated with polyurethane spraying process to improve erosion and corrosion resistance.
4. Vibration exciter: It is composed of special vibration bearing, eccentric pendulum block, magnetic oil plug and other components, and uses splash lubrication to excite. The exciter can work normally under the temperature of -30℃~+80℃, usually with special respirator.
5. Intermediate shaft: Use an intermediate shaft to connect between the two exciters to ensure the synchronous rotation of the left and right exciters. Both ends of the intermediate shaft are connected with the pendulum block of the vibration exciter by a unique elastic rubber disc coupling. The intermediate shaft is a rigid shaft, maintenance-free and without lubrication.
6. Main drive shaft: The main drive shaft is a universal joint shaft that connects the statically fixed installation drive mechanism and the dynamic vibrating screen body.
7. Drive mechanism: The drive mechanism is composed of a motor, a belt drive and a countershaft assembly. The main motor has a large starting torque and fast acceleration, so that the screen machine quickly passes through the resonance zone. The motor is installed on the rail seat to facilitate belt tensioning. The transmission mechanism adopts belt drive to adjust speed and reduce speed, transmit power, and adjust the belt tension with guide rail seat screw tension motor. The countershaft assembly is composed of a countershaft, a bearing, an adapter sleeve, a labyrinth seal and an open bearing seat.
8. Cushioning spring: steel coil spring is used for vibration isolation and cushioning between the vibrating screen body and the installation base. The spring stiffness is small, which reduces the dynamic load on the base. Rubber pads are added at both ends of the spring to reduce the friction and friction noise between the spring and the steel spring seat plate.
9. Screen surface: According to the purpose and user needs, the screen surface adopts different types of sieve plates. The main types are: continuous sieve slotted polyurethane sieve plate, polyurethane frame stainless steel slotted sieve plate, polyurethane frame stainless steel woven sieve plate, polyurethane frame stainless steel punch Hole sieve plate.
2. The operating procedures of the linear dewatering screen:
1. Before driving, check carefully whether the sieve plate is damaged, loose, whether the eccentric shaft bolt is loose, whether there is any debris on the screen surface, whether the chute is unblocked, the water spray device is intact, and no one is working on the equipment.
2. The screen surface should be flat, free from damage or looseness, and the joints should be tight. The sieve holes and sieve slits of the deintermediation sieve should not be too large, small, or excessively worn.
3. The exciter, vibration motor and other lubrication parts should be well lubricated; the support spring should be free from damage, lack and aging failure; all safety facilities should be complete and intact, and comply with relevant regulations.
4. Try to drive without load; the sieve that needs to be sprayed with water should not be blocked, otherwise it should be cleaned immediately.
Three, the start and stop sequence of the linear dewatering screen:
Start sequence:
1. The inspection before the start of the separation screen is completed, and the shift leader or production dispatcher has been given a driving instruction to confirm that the equipment in the next process has been started and operating normally before starting the screen.
2. After the sieve is started, first turn on the water spray and confirm that it is normal before allowing the material to be fed to the screen surface. Adjust the water spray size in time according to the material on the screen surface.
3. After the start-up is completed, perform a comprehensive inspection and make a record of the shift.
parking sequence
1. You must get a parking instruction before you can stop.
2. It must be known that the equipment in the previous process has indeed been stopped.
3. Before stopping, all materials on the screen must be unloaded, and then shut down after turning off the water spray.
Four, operation and maintenance
1. Check the incoming materials, discharge and spray pipes regularly during operation, and report them if they are blocked.
2. Frequently monitor the eccentric shaft, whether the sound is normal, whether the sieve plate is loose, whether there is water running on the sieve surface, report and deal with it in time.
3. During operation, pay attention to check the temperature of each bearing, the temperature of the motor, the sound, the working state of the coupling and the amplitude of the screen under different loads, and report the problem in time.
4. The screen box should vibrate smoothly during operation, and there should be no abnormal swings. If the screen box shakes, check the working conditions of the four support springs and the running direction of the motor.
5. Pay attention to the working conditions of the exciter and the vibration motor during operation. The spindle should rotate flexibly and the bearing should be well lubricated; pay close attention to the bearing temperature.
6. The vibrating screen should regularly check the concentration and particle size composition of the water under the screen to determine the wear of the screen. If the wear is serious, it should be replaced in time.
7. The de-intermediation vibrating screen should adjust the pressure and water volume of the water spray to ensure that the heavy medium of the product on the screen is flushed; often check (see, touch by hand) the de-intermediation effect and moisture of the product on the screen, and adjust according to the inspection result The amount of water sprayed can improve its cleaning effect; closely contact the density control driver to jointly adjust and ensure the deintermediation effect and dehydration effect of the deintermediation screen.
8. The technical indicators of de-intermediation and dewatering include: unit consumption of water spray, concentration of under-sieve and super-grain content, product on-screen and moisture. The driver should strive to complete the above-mentioned indicators stipulated by the factory.
Five, the main measures to complete the index of removal of referral and dehydration
1. In order to strengthen the maintenance of the equipment, keep the vibrating screen in a good working condition; clean the nozzles frequently to ensure uniform spraying; strengthen the management of the screen surface and observe the dynamics during operation. After parking, check frequently, clean up frequently, fill loopholes frequently, and clear blockage frequently to ensure the effective separation (water) area of the screen surface.
2. It is strictly forbidden to put the scattered coal into the funnel under the sieve; it is strictly forbidden to run without water.
3. Regularly check, adjust and replace the coupling and support spring; clean the screen surface and chute; check the tightness of the screen surface, and deal with it if it is loose.
4. Sebenzisa isikhathi sokupaka ukwenza ukugcinwa kwemishini, futhi ubhekane nezinkinga ezenzeka ngesikhathi sokusebenza bese uhlole ngemuva kokupaka.
5. Yenza umsebenzi omuhle ezintweni zokusebenza kanye nokukhucululwa kwendle kwemvelo, gcwalisa ilog yomsebenzi njengoba kudingeka, futhi wenze umsebenzi omuhle wokushintsha amashifu.