What are the sieve methods of linear vibrating screen?
The linear vibrating screen uses a vibrating motor as the source of vibration, so that the material is thrown up on the screen while moving forward in a straight line. The material enters the inlet of the screening machine evenly from the feeder, and generates data through the multi-layer screen. The oversieve and undersieve of various specifications are discharged from their respective outlets. It has low energy consumption, high output, simple structure, easy maintenance, fully enclosed structure, no dust spillage, automatic discharge, and is more suitable for assembly line operations. So do you know what are the sieving methods of the linear vibrating screen? Let me explain it to you next. In the sieving process of materials, the powder sample is passed through a series of standard sieves with different sieve holes, separated into several particle grades, and weighed separately. The particle size distribution expressed as a mass percentage is called the sieve analysis method. That is, sieve analysis, the purpose of which is to determine the particle size composition of the material. There are three common screening methods; these three screening methods can roughly meet the screening requirements of users for different materials. The linear vibrating sieve analysis method can be divided into several types, such as dry sieving, wet sieving, hand sieving, dry and wet mixing, mechanical sieving, air jet sieving, acoustic sieving, panning sieving and self-organizing sieving. And so on, the results of sieve analysis often use frequency distribution and cumulative distribution to express the particle size distribution. There are many methods mentioned above, it depends on which material the user screens, so as to choose the appropriate screening method, but the more commonly used are the first three, let’s take a look together next.
1. Dry sieving method
The so-called dry sieving method, as the name implies, is to calculate the difference between the sum of the sieving balance and the bottom inventory of each sieving meter and the total dry mass m0 of the sample before sieving, as the loss during sieving, and calculate the loss rate. A certain weight of powder sample in the sieve is used to make the fine powder pass through the sieve with the help of mechanical vibration or manual tapping until the sieving is completed. The sieve residue of the powder sample is calculated according to the weight of the residue on the sieve and the weight of the sample. When determining the particle size distribution, dry sieving is generally used.
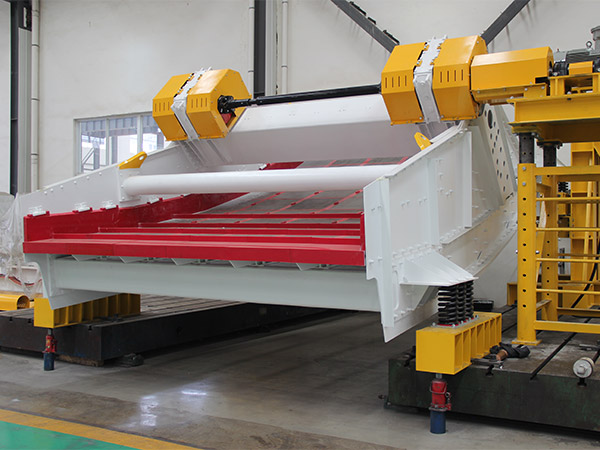
2. Wet sieve method
Put a certain weight of powder sample in the sieve and wash it for a certain period of time with a suitable dispersion water stream (with a certain water pressure), and then the sieving is complete. According to the weight of the sieve residue and the weight of the sample, the wet sieve method is used to obtain the sieve residue of the powder sample. If the sample contains more water and the particles have strong cohesiveness, wet sieving should be used (the accuracy is higher than that of dry sieving), especially for materials with finer particles. If it is allowed to mix with water, it is best to use wet sieving. . Because the wet method can prevent very fine particles from adhering to the sieve holes and blocking the sieve holes. In addition, the wet method is not affected by the material temperature and atmospheric humidity, and the wet method can also improve the operating conditions. Therefore, the wet method and the thousand method have been listed as the national standard method for the determination of the fineness of cement and raw materials.
3. Combined sieve analysis of wet and dry
Combined dry-wet sieve analysis is to combine the two methods and choose the best. When the material contains more water and mud, and the materials are bonded to each other, the combined dry-wet sieve analysis method should be used, and the results obtained by the sieve analysis are more accurate. . The specific method is to pour the sample into a fine-hole sieve and screen it in a basin containing water. Change the water in the basin every 1 to 2 minutes until the water in the basin is no longer turbid. The material on the sieve is dried and weighed, and the quality of the washed fine mud is calculated based on the difference between the weighed mass and the mass of the original sample.
The three screening methods mentioned above use simple equipment and easy operation, but the screening results are easily affected by the shape of the particles. The size of the particle size distribution is relatively coarse. When the lower limit of the test exceeds a certain value, the screening time will be reduced. Extending, it is easy to block the screen. Therefore, when screening, the particle size of the material should be adjusted as much as possible to avoid the material from blocking the screen.